How to prevent a lithium battery fire
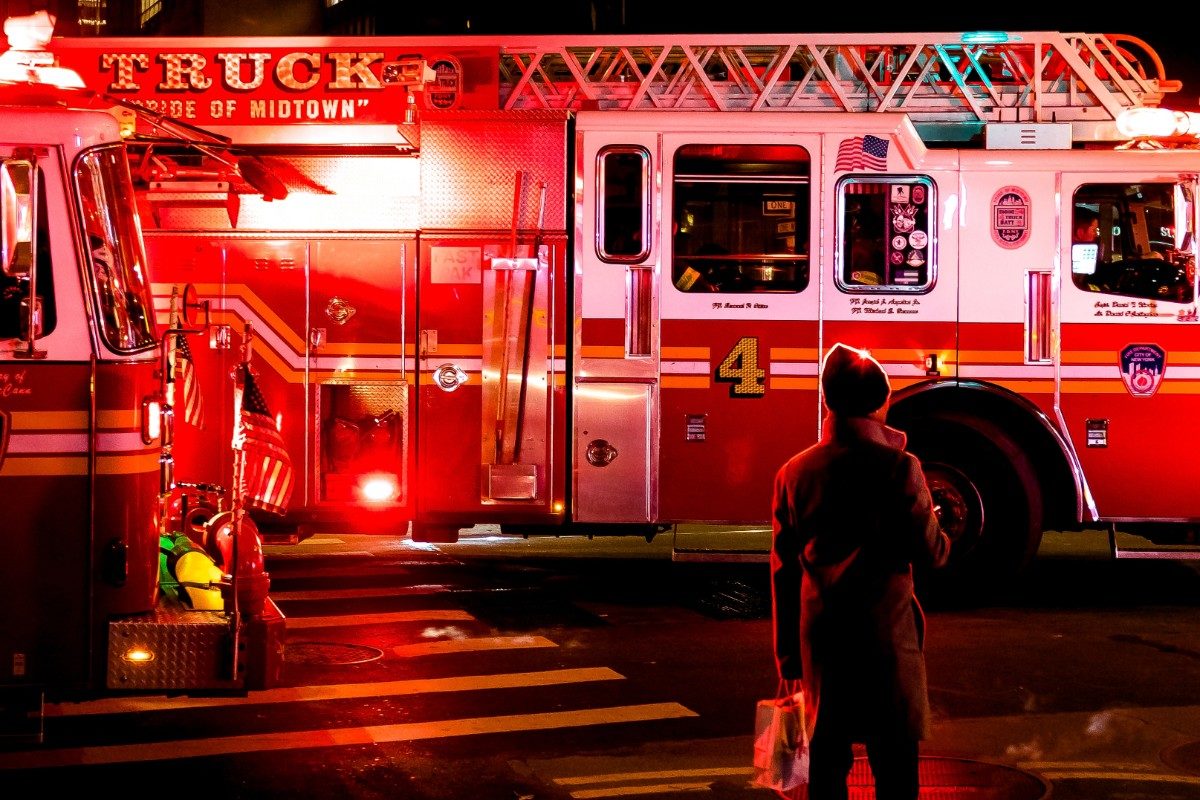
This post was written by Josh Weiner, Solar Expert Witness & Solar Engineering Expert and leads a discussion about safety in energy storage projects. Mr. Weiner has been at the forefront of the solar industry for over 20 years and is an industry leader on solar-plus-storage engineering & design. Josh’s expertise spans both in-front of and behind-the-meter initiatives including residential, commercial, utility, grid-scale, and ev charging solar and storage applications.
A recent Greentech Media article brought to light new details about a lithium battery fire at the Arizona Public Service (APS) McMicken Energy Storage facility that occurred in April.
According to GTM, the fire involved a thermal event affecting one battery rack but not a thermal runaway event affecting multiple battery racks. This is very good news, as we’ll explain below. The article also suggests that venting energy storage enclosures to release combustible gases may be a solution. We respectfully disagree.
A few months after the fire, we gave some initial suggestions on how project managers can design risk out of energy storage systems. This post presents our take on the facts as we now understand them.
We still don’t know the root cause of the fire. However, we know enough to conclude that more ventilation is not the best approach to battery fire prevention. We also know that storage projects need a failure plan, and they need to comply with higher standards.
Read on for our recommendations to help energy storage contractors prevent lithium battery fires.
No thermal runaway
After the Arizona fire, an investigation from APS and battery provider Fluence found that only one battery rack containing 14 modules had “melted.” Evidently the fire did not spread to adjacent racks, setting up a more hazardous thermal runaway scenario, which could have added to the fire’s propagation many times over.
This is encouraging. It’s not the failure of a single cell, but rather the propagation of that failed cell that causes all the damage we see in lithium fires. We should understand why the propagation stopped at the rack level. Here are a few possibilities.
(A) The spacing between racks in the system design was wide enough to stop the fire’s propagation in other racks.
(B) The original equipment manufacturer’s design of the battery pack itself helped prevent rack-to-rack propagation.
As the investigation proceeds, we hope to understand not only the root cause of the APS fire but also the design criteria that helped prevent rack-to-rack thermal runaway. APS is reporting investigation updates here. Independent research and third-party lab testing can also produce findings that improve design and engineering for battery safety.
Venting is not the answer
APS director of technology innovation and integration Scott Bordenkircher told GTM that the McMicken facility fire will prompt engineering and design changes, balancing fire suppression with the removal of explosive gases.
A better answer might be to make sure fire response professionals do not open containers designed to enclose and isolate what’s inside. Do we know enough today to arm firefighters with the correct training to protect themselves and suppress fire? A system designed to fully contain explosive gases may be part of the solution rather than the problem. While investigating ways to improve lithium battery safety, it’s also a good idea to explore best practices for first responders.
Root cause unknown
While it is encouraging that rack-to-rack propagation did not occur, the root cause of the APS fire is still unknown. A root cause analysis will help engineers modify future designs to improve lithium battery safety. Following the chain of events backwards to the point of origin (modules within the rack, cells within the module, and down to the cell level) can yield key insights.
If the root cause of the fire was truly “spontaneous,” which is a real possibility when large quantities of lithium cells are manufactured, no design or manufacturing changes can eliminate the possibility of another freak accident occurring. We may have to accept that spontaneous lithium failures are inherent in lithium technology and manufacturing processes. If this is the case, the best we can do is focus on controllable areas of fire suppression, isolation, and safety at the component- and system-level, rather than at the cell- or module-level.
With that in mind, what can energy storage companies do to eliminate or mitigate lithium battery fires? Here are two recommendations.
Plan for failure
In the event of a lithium battery fire, projects need clear and well-documented protocols to assist in fire suppression, cleanup, and investigation. These prevention and remediation plans ought to be provided as part of the project-specific safety plan or permitting process. This would ensure the information is provided to local authorities and site personnel. System design should also be informed by the possibility of system-level or component-level failures. Fire, building, chemical, and electrical safety codes and standards may be consulted and referenced.
For instance, in the APS fire, the bad rack was positioned in the middle of several batteries that maintained a 90% state of charge. As a result, the APS/Fluence team spent 9 weeks removing and de-energizing all of those batteries.
“There was absolutely no playbook,” Bordenkircher told GTM.
If this experience leads to the creation of a proactive project failure plan, that would be a positive outcome. It could help guide future safety code iterations and standards development.
In addition, it is interesting that APS used LG Chem batteries. According to SepiSolar research, LG Chem batteries have among the widest temperature range needed to initiate thermal runaway. LG Chem batteries also have a fire incident history that reportedly led the battery maker to shut down some of its own storage systems in South Korea.
Raise project standards
The risk of a lithium battery fire is lower in residential and commercial applications than in utility installations. The reason: such projects must comply with the UL 9540 and NFPA 855 safety standards. Utility projects, on the other hand, are basically self-regulating.
UL 9540 addresses construction, performance, and testing of energy storage systems, including how the system handles combustible concentrations and fire detection and suppression.
If we hold utility projects to higher safety standards, battery fire risks will go down.
Improve risk management
It’s more important than ever to understand and manage the risks associated with energy storage projects. That’s why SepiSolar is writing about the APS battery fire and why we will continue to write about it.
Our experience balancing cost, speed, and safety in energy storage projects contributed to the development of the new C&I Project Risk Management Guide. Download a free copy today.
Feature photo by Constante Ken Lim.